Natural Dyes
I am going to talk to you this afternoon about my practical experiences in trying to dye yarns with eucalyptus leaves.
My involvement with spinning, dyeing and weaving began ten years ago. I commenced weaving first and then through frustration of not being able to obtain yarns in the colours and textures I wanted I learnt to spin and commenced dyeing.
I use acid milling dyes and what I realise now was a most amateurish effort and at the same time I started reading about natural dyes. I obtained the New Zealand Dyer Ann Millner’s Book, ‘Natural Wool Dyes and Recipes’, and this was a fortunate choice. I still think it one of the best books for a beginner. I also found Fred Gerber’s articles in ‘Hardweaver and Craftsman’, an American Journal no longer being published and also several articles by Fred in the New Zealand Journal, ‘The Web’. I realised there was a great deal more to the art of natural dyeing than just following recipes, and that it was in fact also a chemical process, and to produce good realiable results I would need to go into it all much more thoroughly.
I saw that Fred Gerber was to conduct a Natural Dye Workshop for the America Handweavers 1978 Convergence to be held in Pittsburg, Pennsylvania, and I enrolled.
As many of you will remember I came home so excited with all my samples from that Workshop and have worked hard since then to produce colours in natural dyes which will equal the best synthetic dyeing in beauty and reliability . Of great interest to me in that Workshop was a series of time testing experiments using eucalypts leaves as a substantive dye. I knew very little about dyeing with eucalypts, I had read the Guild book and realised a premordanting procedure had been used, and was surprised to see that eucalypts gives a substantive dye.
However, a friend gave me an article written by Mikki Glasson from the ‘New South Wales Quarterly Guild Journal’ on dyeing with eucalypt leaves as a substantive dye and I have recently read her book, ‘A Eucalypt Dyers Handbook’ with great interest.
Being a weaver using reasonably large quantities of yarn I found difficulties in consistently getting good results especially with hand spun yarn. It is quite easy with one or two ounces of handspun, but a pound or more is not so easy. The following comments are about some of the experiments I have done to help solve these problems.
I knew that my two gallon enamel buckets were not adequate but I was fortunate in being given a four gallon stainless steal pot which will dye about eight ounces very well. The problem with eucalypt dyeing is that the leaves are bulky and with water, eight ounces seems to be about the limit to get good results in a four gallon pot, but this was an improvement. I then brought an army disposals tea urn which is similar to an electric copper which I use now for larger quantities.
I used reasonably fine fleece which most books fine fleece which most books tell you is more difficult to dye than coarser breeds. However, I found this not to be the case. Fine breeds do need to be handled with more respect. It is important not to agitate the dye bath with vigorous stiring or to let it boil rapidly. I did a series of experiment using eucalypts which give the orange to red colours - as substantive dyes with five different reasonably fine fleeces. I have not used super fine merino. I remove the samples after dyeing for two hours and then four hours. You will see the results of the experiments in the book there (on view during the lecture). I realised immediately that it took four hours dyeing time to obtain a really thorough penetration of the colour. I was using a ration of 4 to 1 dye stuff to wool, and I learnt from Mikki Glasson’s book, she uses a ratio of 10 to 1 and she achieves deep shades with the much shorter dyeing time.
I also realised that I was getting the best results with Wendy Dennis’ rugged Polwarth fleece. Wendy uses sheep coats for her Polwarth sheep to produce high quality fleece for handspinners. This protection of the fleece must be the reason the dye penetrates more easily. I found also that at times the leaves gave better colours and so I started a series of experiments with three different species of eucalypts (En. melliodara) Yellow box, Eu. polyanthemos Red Box, Eu. bauerana Fuzzy box. I obtained the leaves from the same trees every three months, and I have done this for three years trying to keep the experiments as controlled as possible. I found a great variation in shades, and my impression is that the end of winter and early spring is the best time for strong colour. However, after hearing Jean Carman and Dr. Churchill yesterday I realised I have’t enough information to reach any conclusion but the results of my experiments are in the book.
As a weaver it was most important to make sure my yarns were lightfast and washfast. Washfast tests were successful and there was absolutely no problem. I carried out home testing of the dye to lightfastness and felt fairly confident but I wanted to be absolutely sure. John Noble, Lecturer at the Melbourne College of Textiles ran some tests for me under conditions required by Industry and I was absolutely shattered by the first results. The samples stated to fade badly by standard 3 and by standard 7 was practically bleached. For comparison, the clothing industry for women’s clothing uses a standard 4 to 5 I believe and at least standard 7 for rugs and upholstery fabric, so I knew at once that this was not good enough.
In 1978 I was fortunate in being able to attend again the American Handweavers Convergence and I did a Workshop on Synthetic Dyeing with Anoton Viditz-Ward, an Industrial Chemist with Dupont. I spoke to him about the problem of lightfast results and he siad that’s easily solved if you put your yarns in an afterbath of chrome as if often done in the industry. I did more samples for John Noble giving the yarn after dyeing a postmordant bath with chrome, using half the smount of the standard recipe for premordanting with chrome. I bring the dyebath up to temperature of 90°C for fifteen minutes and then let the yarns cool in the dyebath. The tests were then quite satisfactory and reached standard 8 before any chance of fading commenced. So I feel confident the yarn would be perfectly satisfactory from a light fastness point of view, for upholstery fabric, rugs, tapestries, or any article exposed to strong sunlight.
These sample skeins were dyed with eucalypt polyanthemos and you can see quite clearly the slight darkening after the chrome treatment.
I feel this is quite an acceptable difference to have lightfast yarn. I have developed a fairly routine method now for my own use. I use only the leaves at a ratio of usually 4 to 1 dyestuff to wool. The leaves are soaked overnight in hot water, next day slowly brought to the boil, kept at a simmer for one hour. The yarn is the added and kept at a temp of 90°C or 190°F for 2 to 4 hours depending on the depth of colour required. Sometimes the red dye doesn’t appear to be released into the dyebath for up to 2 hours. When possible I leave the yarn to cool in the dye-bath. I then do any post-mordanting using tin, copper, or iron for a range of shades, and the chrome after treatment for lightfastness. I have found that 1/2 cup of vinegar in the last rinse helps to restore the lustre of the fleece.
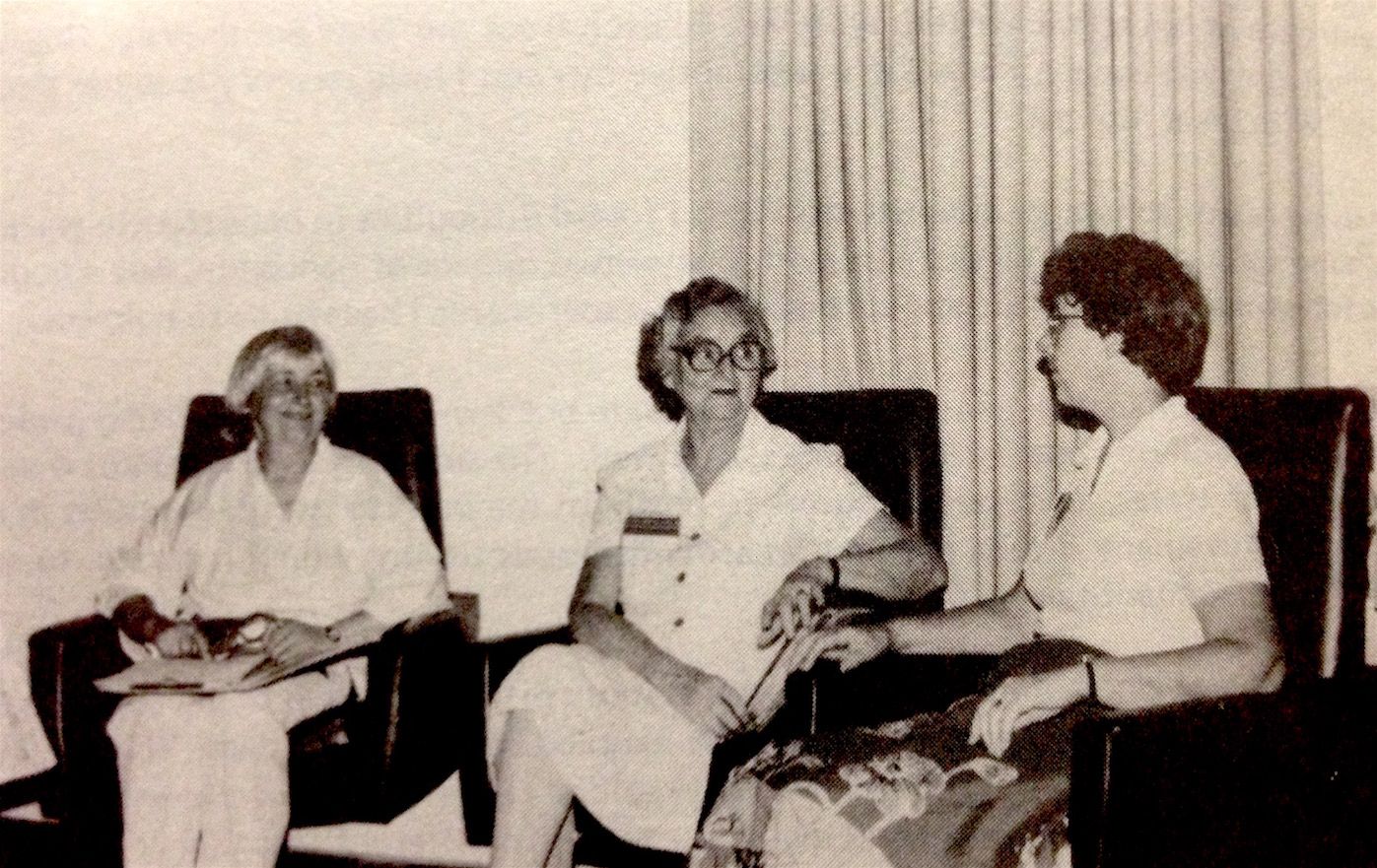